Managing a warehouse is a complex and multi-levelled process. If you are currently managing a warehouse, you will already be familiar with the different costs involved and how ordering and selling inventory go way beyond the purchase price of each item, and that these additional costs need to be managed to ensure that your business remains profitable.
There are many aspects that need to be managed when it comes to inventory processing, and being able to identify and quantify each of these aspects are cost-saving opportunities. However, difficulties can arise when you are unable to differentiate between them or even worse, be unable to identify them in the first place.
There are many different types of costs associated with inventory management, but for today, we are going to explore the three major ones.
Inventory Costs – What are they?
Carrying Costs
Warehouse inventory involves capital that you may not even realise has a direct link or association with your stock. You need to consider where your stock will be stored, the utilities involved for your premises e.g. lighting, heating, air conditioning, as well as insurance and staffing. Typically, the greater the amount of inventory the greater the carrying costs and these costs can slowly erode the value of your inventory if the carrying costs have not been identified.
There are also other costs that are associated with carrying inventory. If you are managing a warehouse, you generally have a good idea of what your stock movements, are and which items of stock are fast-selling and which usually hang around in stock for longer. However, holding stock over a long period increases the risk of inventory shrinkage and obsolescence.
Inventory shrinkage simply means your total item stock count has shrunk over time and this can occur for several reasons such as damage, misplacing of goods, stolen items and waste. Obsolescence is when your stock becomes outdated or no longer of use; this particularly important for perishable good and expiry dated items.
By integrating our Bit Inventory with your existing Sage Accounts, our advanced functionality can help you to avoid these issues by easily keeping up to date with stock rotation. For items that are not limited by expiry dates, you may face other issues such as seasonal or fashion trends, where the cost of your inventory is tied up and cannot be reinvested elsewhere.
‘Sold-out’ Costs
There are many ways to try and reduce the costs of carrying inventory and many warehouses utilise the just-in-time stock approach. Though this method can be successful in reducing costs, there are many risks associated with this. The just-in-time approach does not account for the spike in sales such as seasonal trends and more often than not can leave you with out of stock items.
Out of stock items can have major implications on your business, leaving you with empty shelves or warehouse space, as well as reducing customer confidence and satisfaction. However, by integrating inventory management solutions such as Bit Inventory 50 or Bit Inventory 200 to your Sage Accounts you could prevent these issues. From order processing through to receiving goods, dispatching and stock taking, our Sage inventory solution makes your process efficient, accurate and eliminates human errors.
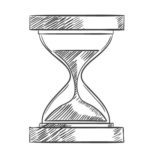
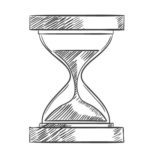
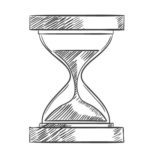
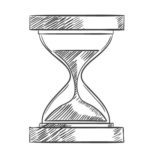
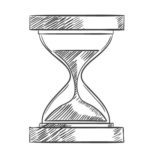
Ordering Costs
In addition to the purchase cost of inventory, there are other costs to consider such as the procurement of the inventory, for example, the delivery, the labour of transporting and transferring stock, as well as the overall management of the stock process and the downtime costs for manual stock takes. By not having the right systems, these processes can be left open to human error. The question is, how much control do you really have over your stock inventory processes? Our Sage integrated inventory management solution can help you take back control.
Reducing Inventory Costs – What are the best practices?
Having an insight into your warehouse is vital but knowing how to manage it and how to assess the hidden costs is even more important. Real-time data can help ensure that your procurement is linked to demand, order processing, and is tailored to your customer needs.
Greater automation can help reduce staffing costs and human errors and give you real-time oversight of your inventory levels.
Get in touch today to find out how we can help you maximise this powerful inventory management solution.